150 Ton Crane Failure!
The Maintenance Manager for a local steel manufacturer has the challenging responsibility for maintaining the life and uptime of the company’s critical specialty steel production equipment. Of particular importance are the two 150 ton overhead cranes integral to the melt shop production area, along with the other 40+ cranes and hoists supporting sub processes throughout the rest of the facility. Part of the system in place to maintain the cranes, was yearly inspections performed by Zelus technicians to ensure safe function, as mandated by the ministry.
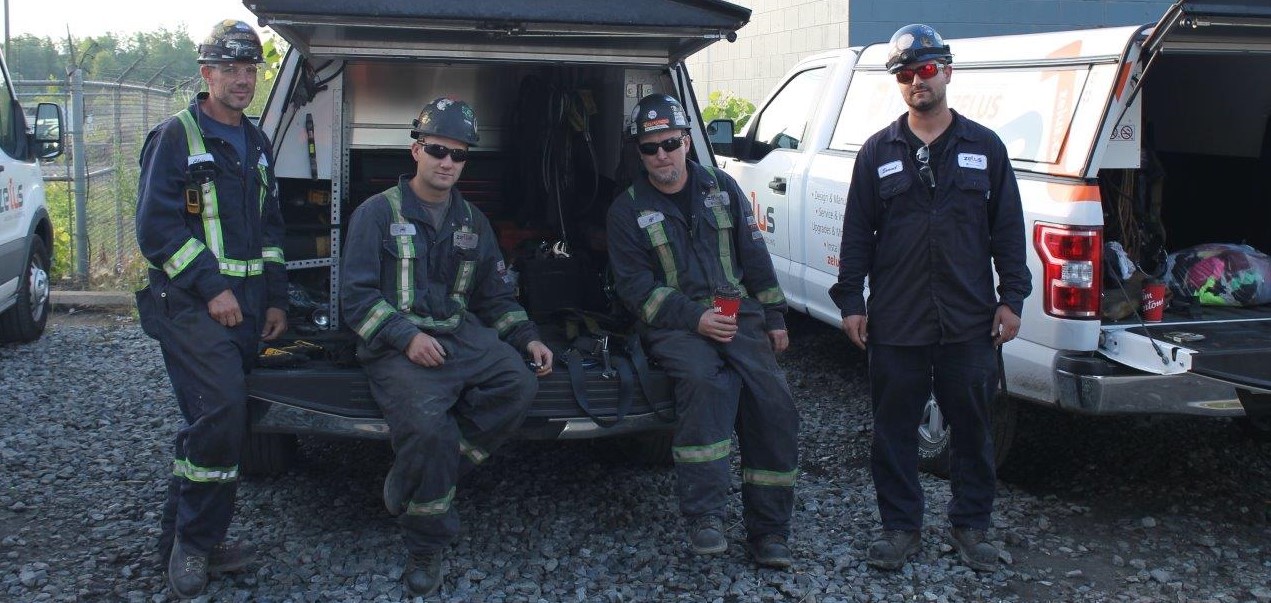
Need a crane you can call your own?
Unfortunately, just before the yearly inspections scheduled due date, a upper limit switch had failed allowing the hook to travel past the high position for one of the two 150 Ton melt shop cranes. This failure caused significant damage and a dangerous situation. The hoist was left inoperable, and one of the company’s main production cranes was now out of service. Thankfully, no one was injured in the event.
With one of two melt shop cranes down their production capacity was limited. The custom 150 Ton hoists used for these cranes were custom and the delivery for a new replacement would be many months. He determined a repair of the hoist was clearly his best strategy and he reached out to Zelus to see what his options were for getting his crane back in operation.
The Maintenance Manager had chosen Zelus for the ongoing maintenance for these specialty cranes and fortunately this gave Zelus an advanced understanding of how these cranes operated and their importance to their operations. The Maintenance Manager made sure Zelus was at their facility quickly and arranged to meet with the management team. He quickly provided Zelus with drawings of the crane, as well as a mobile crane and man lifts so technicians could access the site and start to understand the depth of damage to his hoist.
Immediately, and quite clearly, it was found that the main structure of the hoist and trolley was severely damaged by they hook block driving into the underside of the hoist/trolley. Due to the extreme loading applied during the accident, disassembly and inspection of all internal components was required. This determined that along with the hoist/trolley structure, the replacement of the dead end, equalizers, wire ropes, damaged bearings, shafts and related components was also required.
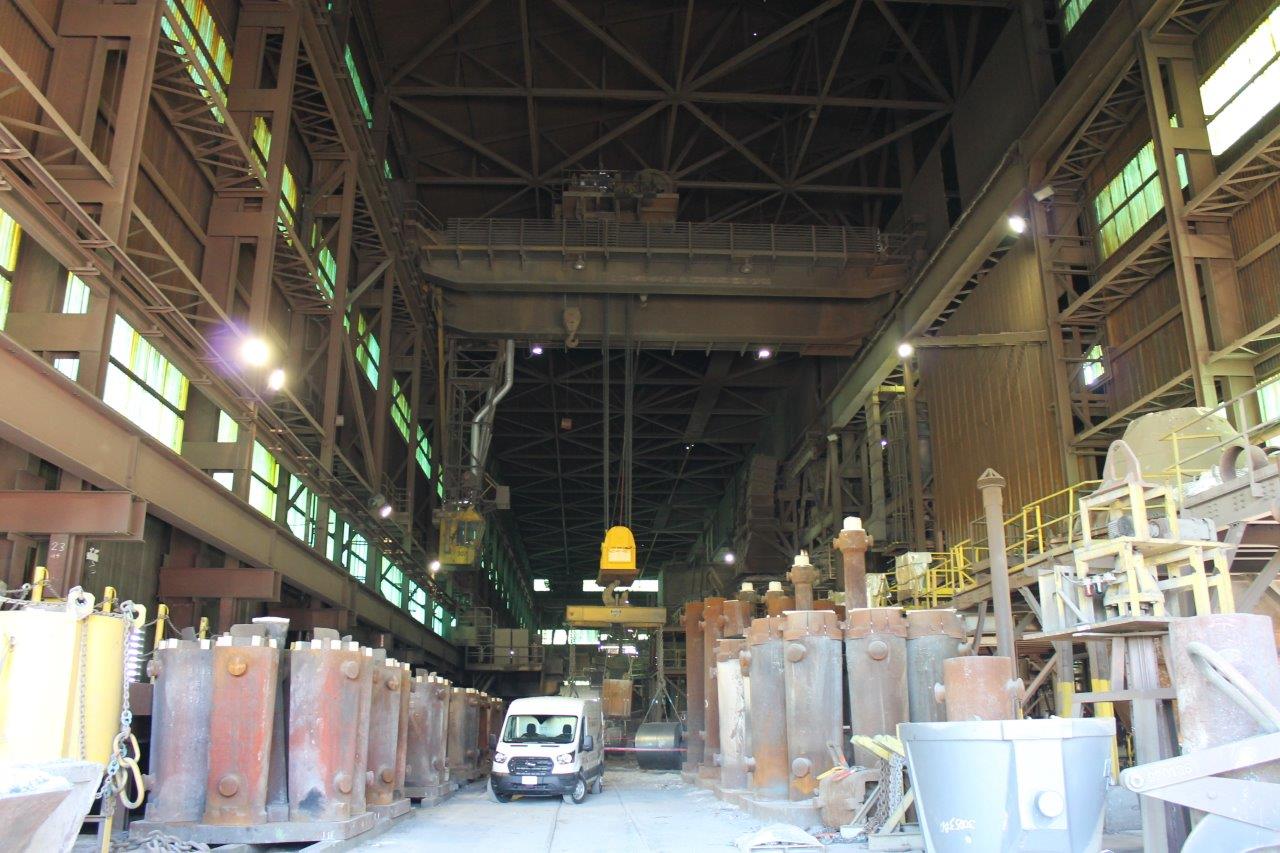
This repair was multi faceted and was not going to be an easy undertaking. It would require engineering to design components that are not available off the shelf, fabrication of those components, identification and procurement of standard parts, and co-ordination of several technicians and equipment over many days in a production environment. This was a demanding situation for both the manufacturer and Zelus. The Maintenance Manager developed a plan with Zelus and his team, to determine the best course of action.
Engineering and procurement was expedited, and after all parts were in, the lower and upper block assemblies, power limits and cable reel were rebuilt. The new hoist/trolley load beam was manufactured and it was also ready for installation. Traditional course of action would be to remove the hoist and drop it to the ground for repairs. In this case a plan was developed to complete the repairs while in position on the crane, reducing the amount of lifting equipment required for the removal of the heavy hoist, as well as limiting the impact on production and valuable floor space. This was estimated to save approximately 50% of the overall project costs. A team of 4-6 technicians were assembled for 4 weeks to carry out the repairs, load test, and certification to return the crane to operation.
The project was completed under budget, and on time, compared with what was budgeted in the original plan. It is also estimated that 2-4 weeks were saved by leaving the hoist in the air, and over 20 – 26 weeks relative to waiting on a new custom hoist. This was all done while production continued. While this was at a reduced capacity, they were able to continue producing steel during the repairs, and the overall down time was minimized.
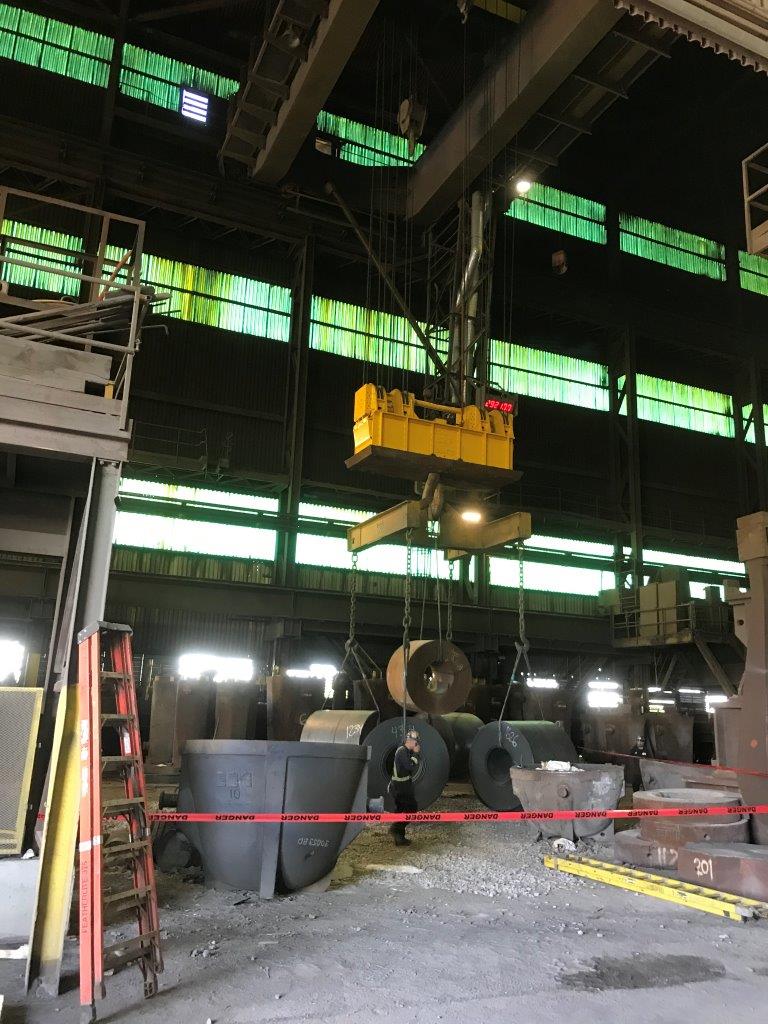
The repair took 4 weeks to complete and required many disciplines of expertise to complete - engineering, manufacturing, service, and installation.
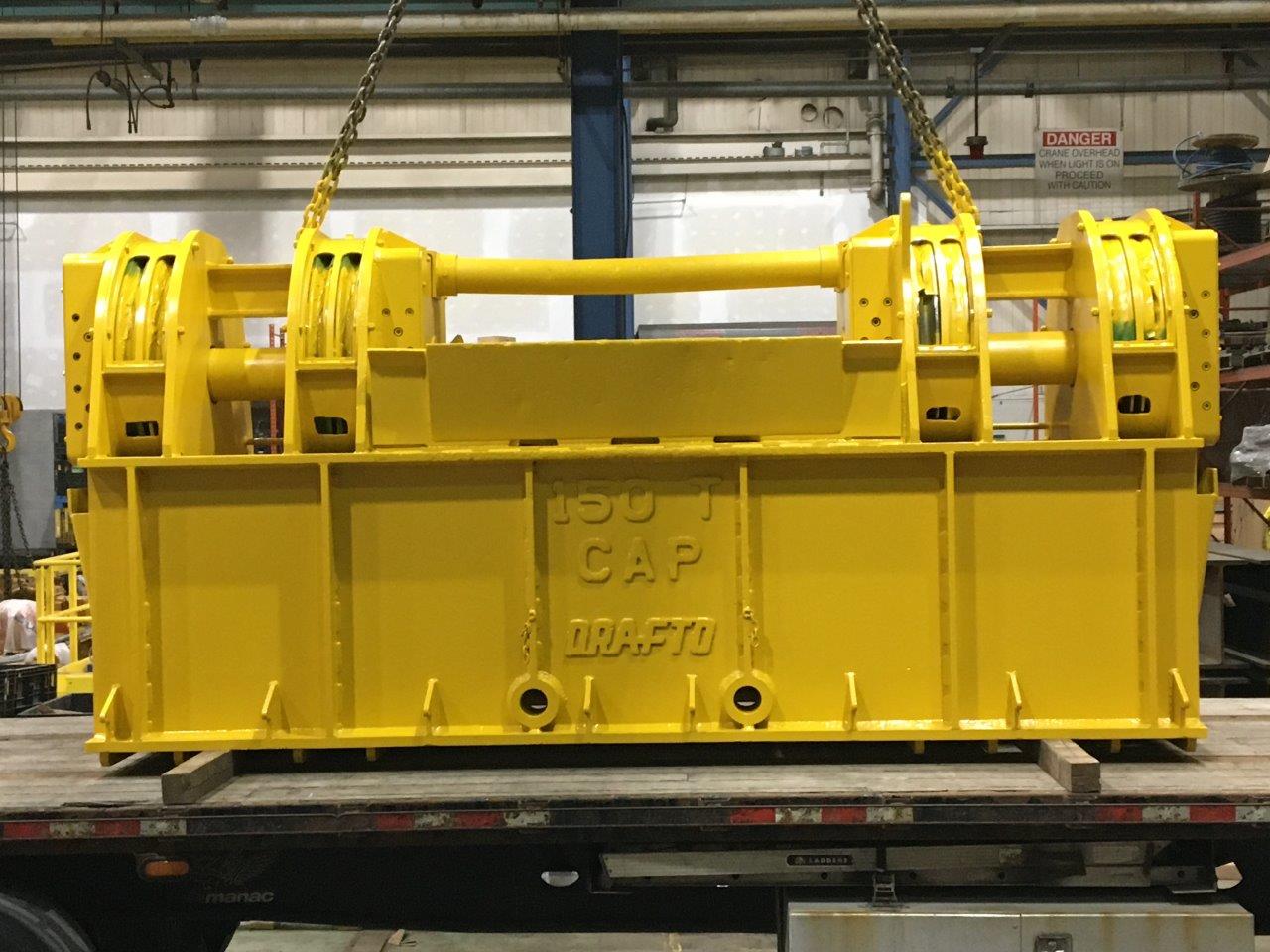